Electrician Tips And Articles For Your Home

Whole Home Generator Myths Busted: What New Haven Homeowners Really Need to Know
When it comes to whole home generators, misinformation can keep homeowners from making smart, protective investments. If you've dismissed the idea of installing one based on cost, location, or noise, it's time to take a second look. Let's bust some of the most common myths about […]
Learn More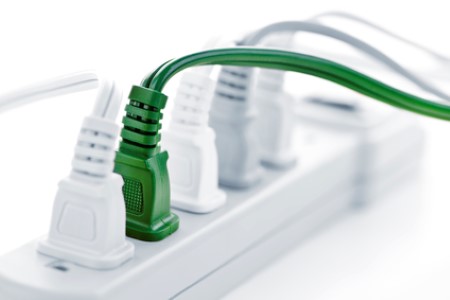
Is Whole Home Surge Protection The Right Solution For Your Home?
Everyday across the country, countless homeowners lose their televisions, game systems, computers, appliances, and a whole host of other electrical devices to power surges. When a power surge hits your home, there is a very high chance that you are going to face more than just […]
Learn More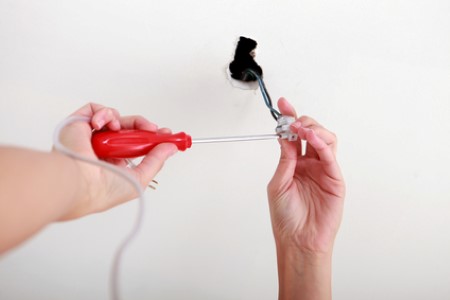
5 Signs It’s Time To Call A Fairfield County Electrician
The best time to call a Fairfield County electrician is when you suspect a problem with your home’s electrical system. Yet, some signs of trouble can be very subtle or seem insignificant when there’s so much else going on in our lives. Electrical Services Group LLC wants […]
Learn More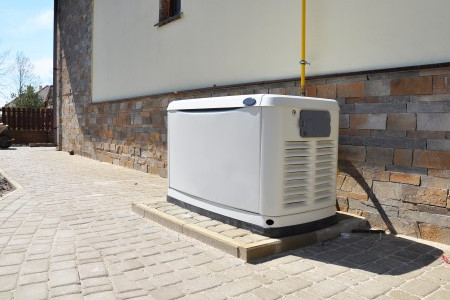
Probable Reasons Why Your New Haven Home’s Backup Generator Aren’t Starting
A backup generator is a great peace-of-mind installation for your New Haven home, as it will allow you to maintain power during any blackout situation. Of course, like anything, your backup generator can develop issues that might prevent it from starting up when you need it. To […]
Learn More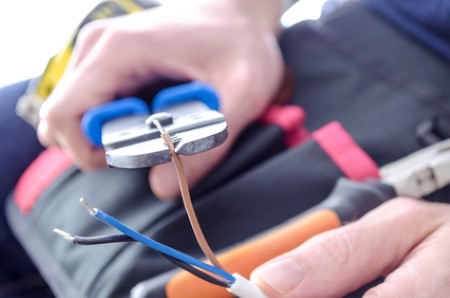
How To Tell If Your House Needs Wiring Repair
The electrical wiring in your home is normally present in every room in the house. 1972 and prior built homes contained wiring which didn’t last as long because it was more susceptible to shorting and wear. The insulation and other materials are likely degraded if your home […]
Learn More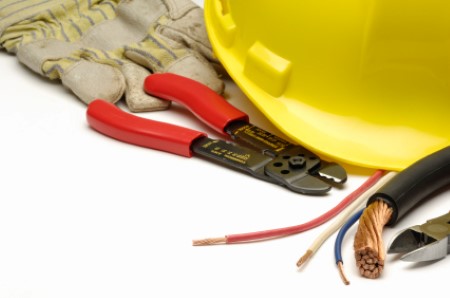
Is Your Home In Need Of A Panel Upgrade?
A panel upgrade is not something that the average homeowner has probably given much thought to. Yet, for the safety of yourself and your loved ones, you most certainly should be. This is especially true if you are a New Haven homeowner with an older house, […]
Learn More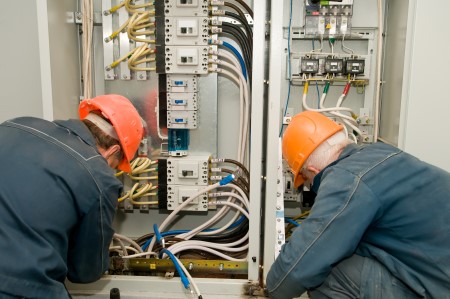
Commercial Electrical Construction Services Customized To Your New Haven Property
As a commercial property owner in New Haven, you have an obligation to ensure that your building or facility is customized to promote the productivity and profitability of your business. One of the most important aspects of your commercial property is its electrical system. When you […]
Learn More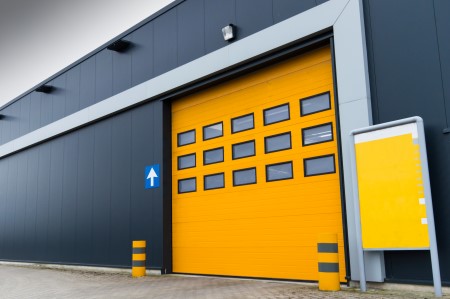
Electrical Safety For Schools, Hospitals, Offices, And Other Institutional & Commercial Entities
Electrical safety couldn’t be more vital if you’re responsible for a New Haven area school, hospital, office, or other commercial or industrial buildings. It’s vital that your electrical repairs and new installations are handled by only experienced, licensed electricians who do the work according to current […]
Learn More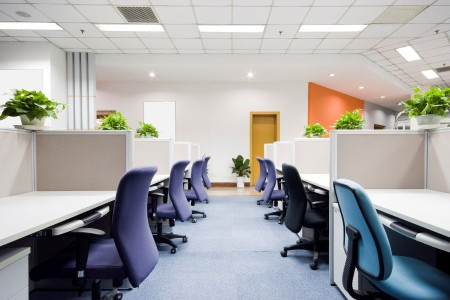
What To Expect During Commercial Electrical Construction
Whether you’re rewiring your building or installing an electrical system for brand new construction in New Haven, commercial projects are far more labor intensive and require more power and heavier equipment than residential projects. So, in effect, your expectations should be higher from start to finish. […]
Learn More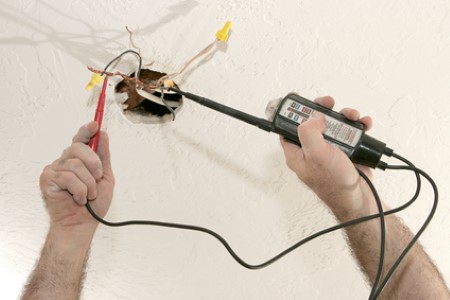
How To Know Your Home Needs New Electrical Wiring
Without a doubt, our residential New Haven electrical systems are largely responsible for the high quality of life that we enjoy. Because electricity has become so ubiquitous, people often take it for granted. Unfortunately, this mindset can be dangerous because all though electricity is everywhere it […]
Learn More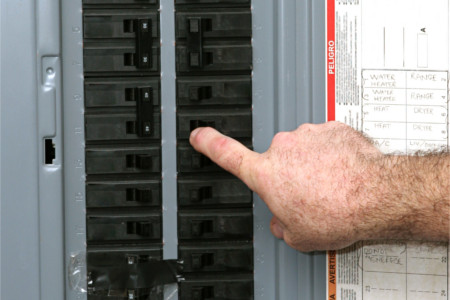
Why Do Circuit Breakers Trip
When a circuit breaker trips in your New Haven home, you’ll have to go outside, out to the garage, or down to your basement in order to switch it back and get the power back on. This can be extremely frustrating, especially if it’s happening over […]
Learn More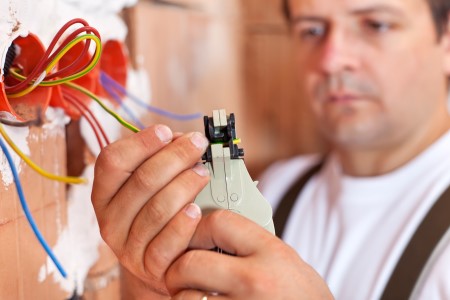
Bridgeport Electrical Rewiring Remodeling
One of the first things you need to consider when you are planning a home renovation is the existing electrical system. Is the condition of the existing electrical wiring and the capacity (in amps) of the system up to code? Along with plumbing and heating and […]
Learn More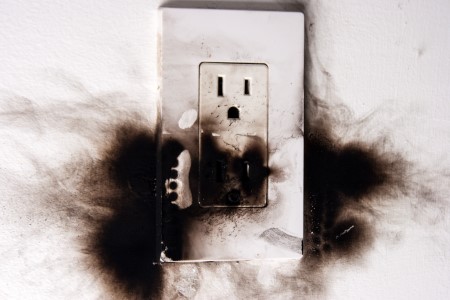
Have The Newtown Professionals Do All Your Electrical Repairs
Most households and buildings regularly require Newtown electrical repairs. This is logical as electricity is always used for operating appliances, equipment, and other machines. Short-circuits and small electrical shocks are normal and are quite usual. However, it is surprising that services of professional electricians are hardly […]
Learn More
Greenwich Panel Upgrades
Encountering flickering lights or appliances that cannot function appropriately are tell-tale signs of an electrical system problem. This situation may require that one seek professional help immediately other than just sizing up the problem yourself that may require more complicated steps to figure out the problem. […]
Learn More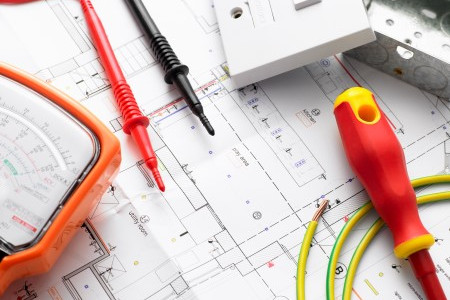
Finding A Commercial Electrician For Your New Haven Business
Starting a small business comes with many headaches, both large and small. If you have built your own building space, or need to make electrical adjustments because of your company needs, you’ll have to find a good commercial electrician. This may be one of the smaller […]
Learn More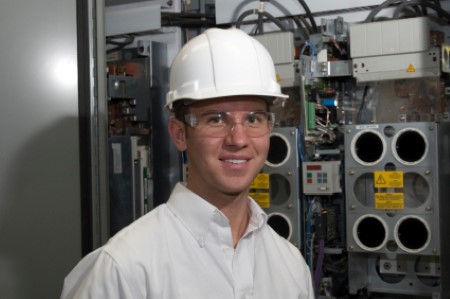
New Haven Commercial Electricians
Commercial electricians specialize in working on industrial buildings, factories, and any other type of commercial property you can imagine. This type of electrical work greatly differs from residential work because of the amount of power that is involved, and because of the code and regulations that […]
Learn More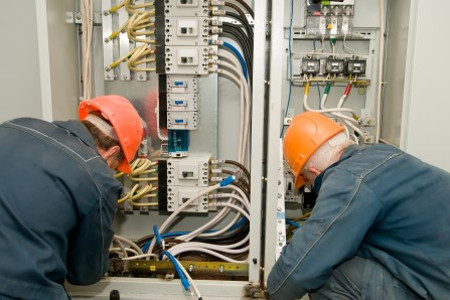
New Haven Commercial Electrical Repair - Hiring A Contractor
As far as some people are concerned, the most important repairs are done in commercial places. This is because commercial institutions are what keeps the business world running. The ‘inviting’ aura of commercial areas should be maintained if these places that exist for profit are to […]
Learn More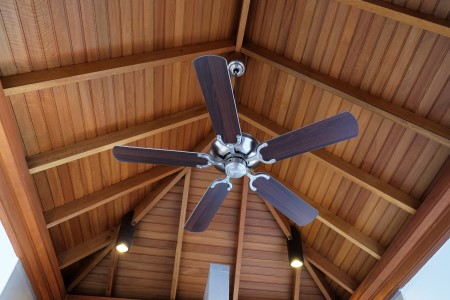
New Haven Ceiling Fan Options
Ceiling fans are electrically-powered fans suspended from the ceiling of your New Haven home. Unlike air conditioners, they do not change air temperature, instead, they circulate air. They only introduce movement to the air through their rotating paddles. There are, however, some fans that reverse the […]
Learn More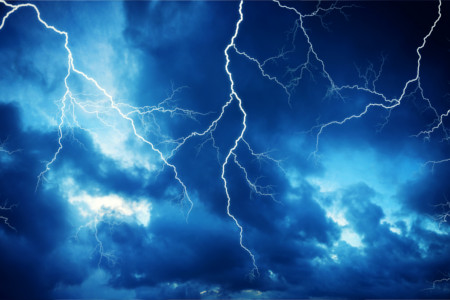
Protecting Your New Haven Electronics
Increasingly, New Haven residents find themselves more and more dependent on electrical devices in this modern world. Our DVD players, gaming systems, microwaves and of course our computers are important to our quality of life and communication with our family, friends and in some cases, work […]
Learn More
The Power Of New Haven Home Generators
Home generators are one of the most useful machines ever invented. Because of the rapidly evolving technology, people have grown accustomed to making work easier through the use of electricity. In one way or another, electricity is present in almost everything people do – from charging […]
Learn More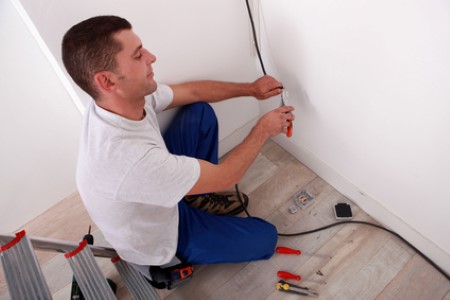
Getting The Best Electrical Contracting Services
In any establishment, electrical works are always a requirement. There is no house, building, industrial plant, or commercial establishment that is ever constructed without electrical services. Generally, electrical work pertains to the lighting and wiring of any establishment. It involves electric fixtures, electric appliances, electric baseboards, […]
Learn More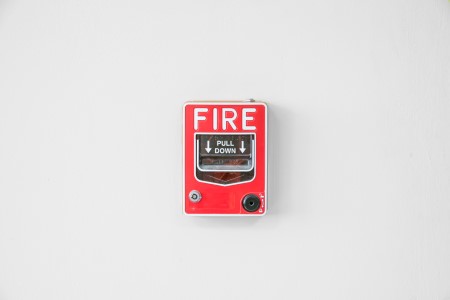
Fundamental Configuration Of A New Haven Fire Alarm System
What is an automatic New Haven fire alarm system? An automatic system that is designed to detect the unwanted fire presence by its monitoring of the changes in environment that are related to combustion. A smoke warning system can be actuated automatically or manually or in […]
Learn More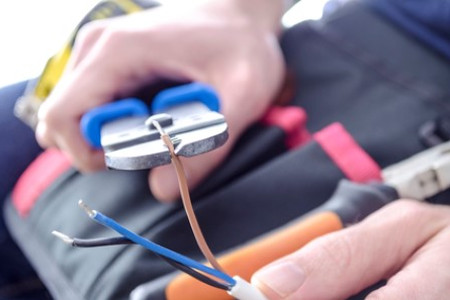
Hiring A New Haven Electrician For Electrical Repairs And Services
For you to be able to ensure that you get the best possible job done in your home, you should limit your options among contractors that will be able to take the best possible care of your home systems. Even if highly skilled professionals tend to […]
Learn More
Why Electrical Repairs Should Always Be Done By New Haven Electricians
Most households and buildings regularly require electrical repairs. This is logical as electricity is always used for operating appliances, equipment, and other machines. Short-circuits and small electrical shocks are normal and are quite usual. However, it is surprising that services of professional New Haven electricians are […]
Learn More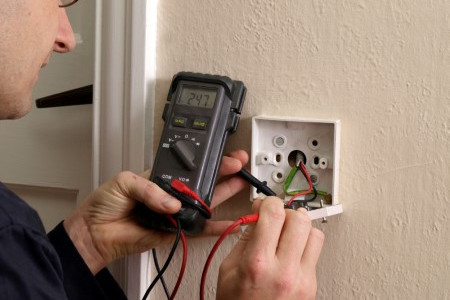
Selecting The Right Electrician Is Vital For Safety
Perhaps, you know some people who have bad experience with regards to hiring a New Haven electrician. Some have problems with exorbitant pricing while others observed poor workmanship. Getting the wrong person who you will let do all electrical related jobs at home can result to […]
Learn More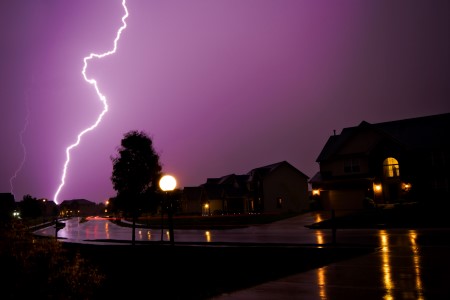
Why Install Surge Protection In New Haven?
Surge protection is something every home should have especially if the homeowner wants to preserve the quality of their appliances. The fact is that the electricity passing through a home is not always constant. It can go up and down due to power outages, downed lines […]
Learn More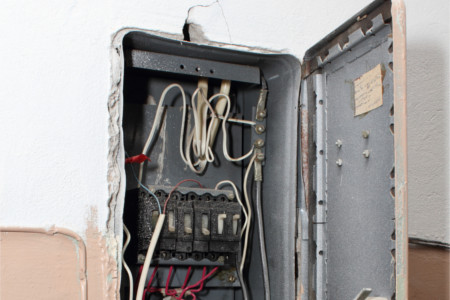
New Haven Panel Upgrades: A Safe Choice
Electricity puts a house in function. It plays a vital role in serving food, keeping us warm from the weather, aiding us in daily tasks and providing comfort with many variables of entertainment. Without it, a house ceases to function effectively. It is with this thought […]
Learn More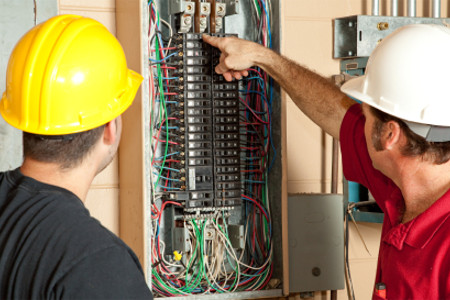
New Haven Panel Upgrades: Why Aren’t You Doing One Already?
There was a time when the only dominant and more energy-consuming electrical appliances in the house are the lights, the TV, the refrigerator and the heater for those cold winter nights. Unfortunately, that was a thing of the past – today, the electric-powered stuff in your […]
Learn More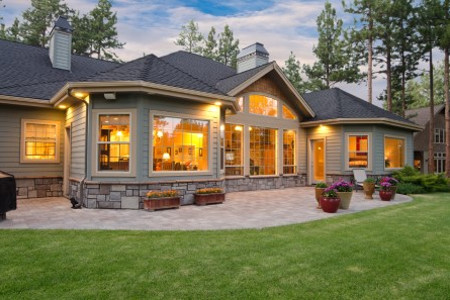
New Haven Generators: Assuring Reliable Energy Source During Emergencies
Significant additions to one’s home bring about improvement to the quality of living for those who reside in it. It can be done for luxury, upkeep, refurbishing, space management, energy conservation, and preparedness for emergencies. Acquiring New Haven generators falls under preparedness for emergencies. With such equipment […]
Learn More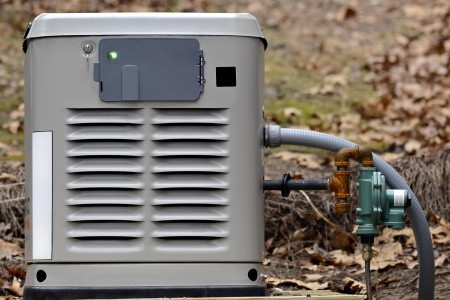
How To Pick Home Generators In New Haven
Home generators are your run-to when there are power interruptions. Not having enough electricity could really make it hard for a household to work as normally as it would want, and this is why it’s important that you choose a generator that is most compatible for […]
Learn More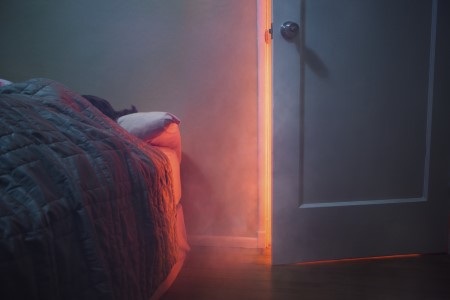
Trusting Homes To Electricians In New Haven
A lot of fires are caused by short-circuits and electrical problems. So for home improvement projects, always look for a New Haven electrician to ensure the safety of homes and of people living on it. One responsibility of electricians is to prepare the electrical installation layout […]
Learn More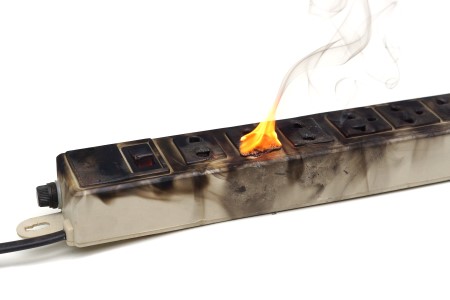
Why Should You Call A New Haven Electrical Contractor?
When the lights go down, whom do you call? No, not Superman, silly, and neither is your Momma. When electricity fails you, it’s not a man in cape that you’d call but him – the New Haven electrical contractor. The switch won’t work? Fuses have blown up […]
Learn More